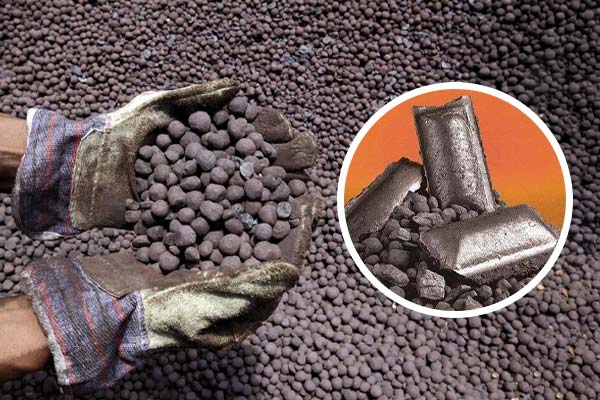
فولاد یا آهن اسفنجی همان گندله متخلخل است که از احیای مستقیم سنگآهن به دست می آید و بهترین جایگزین برای آهن قراضه در کارخانجات تولیدی می باشد و حدود 5 درصد از بازار آهنآلات جهان را تشکیل میدهد و روز به روز در حال افزایش است که اهمیت این محصولات آهنی را در صنایع مختلف نشان می دهد.
در کشور ما نیز استفاده از آهن اسفنجی از سال 89 شروع شده و سومین تولید کننده ی آهن اسفنجی بعد از هندوستان و ونزوئلا در جهان هستیم. اگر شما هم در این حوزه فعالیت می کنید و علاقمند هستید در خصوص فولاد اسفنجی ، ویژگی ها و کاربرد های آن اطلاعات بیشتری کسب کنید؛ دعوت می کنیم در ادامه با فولاد نصر آذربایجان همراه باشید.
آهن اسفنجی چیست (sponge iron) ؟
آهن اسفنجی یا آهن احیای مستقیم(DRI) مادهای است که از احیای سنگآهن (به شکل کلوخه، گلوله یا خاکروبه) به صورت مستقیم یعنی بدون ذوب کردن، به دست میآید. در طی فرآیند احیای مستقیم و به دلیل خروج گاز اکسیژن، سنگآهن به قطعههایی کروی شکل تبدیل میشود که مانند اسفنج در سطح خود دارای سوراخهای کوچکی است. همین ویژگی ظاهری سبب نامگذاری این محصول شده است. همچنین میزان عیار آهن اسفنجی بسیار بالا بوده و چیزی بین67 تا 95 درصد می باشد.
ویژگی های فولاد اسفنجی
از مهم ترین ویژگی های فولاد اسفنجی می توان به موارد زیر اشاره نمود:
- دارای مقادیر بالایی از عنصر آهن بوده و درصد خلوص آن بسیار زیاد است.
- عناصر سمی مثل سرب، قلع، روی، تنگستن در آن کم است.
- از نظر انسجام و یکدست بودن کیفیت بالایی دارد .
- محتوای فسفر و گوگرد آن کم است.
- کمترین میزان گرد و غبار را به خود جذب می کند.
فرمول شیمیایی آهن اسفنجی
آهن اسفنجی تحت واکنش شیمیایی ویژه ای ساخته می شود و فرمول شیمیایی آن به شکل زیر است، البته توجه داشته باشید این واکنش برگشت پذیر است و با یک مرحله انجام نمی شود و برای حذف اکسیژن به صورت تدریجی اکسیدهای گوناگونی تولید می کند.
CO2 + C = 2CO ؛ C + O2 = CO2
FeO + CO2 = Fe (metallic) + CO2 ؛ Fe3O4 +CO +FeO + CO2 ؛ Fe2O3 + O3 = Fe3O4 + Co2
روش های تولید فولاد اسفنجی
تولیدگندله متخلخل از سنگآهن با استفاده از گاز طبیعی یا زغالسنگ انجام میشود. معمولاً در کشورهایی که دارای ذخایر گاز هستند، از روش گازی استفاده میگردد. برای مثال در کارخانجات فولاد خوزستان و فولاد مبارکه از گاز به عنوان ماده احیاکننده استفاده میشود.
استفاده از گاز طبیعی :
برای تولید فولاد اسفنجی به وسیله ی گاز طبیعی معمولا از 3 روش زیر استفاده می شود:
- میدرکس (Midrex) : کم مصرفترین و پر بازدهترین و پر کاربرد ترین روش تولید آهن اسفنجی در ایران و جهان میدرکس است. در این روش گاز متان وارد واحد شکست شده و به دو گاز احیا کننده اکسیژن و هیدروژن تجزیه میشود. سپس در یک کوره استوانه ای دمیده می شود و همزمان سنگ آهن از بالا داخل کوره انداخته میشود تا با گاز متان تجزیه شده برخورد کند. این گاز تجزیه شده هنگامی که در کوره دمیده شد، داغ میشود و سنگهای آهن به هنگام برخورد با آن اکسیژن خود را از دست می دهند. در آخر گلولههایی متخلخل از آهن خالص که پخته و سخت شدهاند تحت عنوان محصول نهایی ارائه میشوند.حدود 80 درصد آهن اسفنجی ایران، به این روش تولید میشود.
- HYL اچ – وای – ای : در روش HYL نیز مانند روش میدرکس، از گاز طبیعی برای احیای سنگ آهن استفاده می شود، با این تفاوت که این روش دارای مصرف برق بالا و مشکلات ظرفیتی است.
- Purofer
استفاده از زغال سنگ :
برای تولید فولاد اسفنجی به وسیله ی زغال سنگ از روش های زیر استفاده می شود:
- SL/RN (اس – ال – آر – ان) : در این روش به جای گاز طبیعی متان از زغال سنگ برای احیای سنگ آهن استفاده می شود. به این صورت که ابتدا مواد اولیه شامل سنگ آهن ، زغال سنگ ، آهک و دولومیت با هم ترکیب شده و برای مرحله احیا به کوره افقی فرستاده می شود. در این مرحله دمای کوره تا حدی بالا میرود که زغال سنگ کک نشود و شروع به سوختن و تولید دی اکسید کربن کند. و تولید دی اکسید کربن آنقدر ادامه پیدا می کند و دما بالا میرود تا سنگ آهن به صورت کامل احیا شود.
- Jindal (جیندال)
- DRC (دی – آر – سی)
نکته : از روش های برمبنای زغال سنگ در ایران استفاده نمی شود.
مزایای آهن اسفنجی
از مهم ترین مزایای فولاد اسفنجی که سبب گسترش استفاده از آن در صنایع مختلف شده است می توان به موارد زیر اشاره کرد:
1- به دلیل کمبود ضایعات آهن و افزایش قیمت آن و همچنین مشکلات زیست محیطی، آهن اسفنجی بهترین جایگزین برای ضایعات است.
2- آهنهای اسفنجی از عیار و خلوص بیشتری نسبت به دیگر محصولات آهنی برخوردار است.
3- انتقال و حمل و نقل آهن اسفنجی به شکل کلوخهشده بسیار آسان و بدون دردسر است.
4-کورههای القایی یا واحدهای احیای مستقیم، هزینه کمتری نسبت به کورههای بلند دارند.
5- برای تولید آهن اسفنجی به روش مستقیم میتوان از گاز طبیعی بدون جداسازی ناخالصیها استفاده کرد.
6- آهنهای اسفنجی از بازدهی بالایی برخوردار است و صرفه ی اقتصادی خوبی را به همراه دارد.
خطرات آهن اسفنجی
آهن اسفنجی با وجود مزایای فراوانی که دارد، در صورت عدم محافظت در معرض اکسیداسیون و زنگزدگی است، و به طور معمول با سرعت بیشتری نسبت به فولاد خورده میشود. همچنین برخلاف آهن چدن کورهای که تقریباً از فلز خالص است، آهن احیای مستقیم حاوی مقداری ناخالصی سیلیسی است که در فرآیند ساخت فولاد باید از بین برود.
از دیگر معایب آهن اسفنجی میتوان به امکان اشتعال آن در حالت خمیری اشاره نمود. که برای رفع این مشکلات نیاز است تا در اسرع وقت این محصول به فولاد تبدیل شود و یا حفاظی برای آن در نظر گرفته شود.
کاربرد های آهن اسفنجی
از مهم ترین کاربرد های آهن اسفنجی میتوان مواد زیر را ذکر کرد:
- استفاده در کوره القائی به طوری که که توانسته جایگزین حدود 50 درصد قراضه شود.
- پس از ذوب و احیا در فولادسازی، در فرآیند ریختهگری به شکل اسلب (تختال)، بیلت( شمش) و میلگرد درمی آید.
- در تولید آهن فرفورژه یا فولاد فرآوری شده استفاده می شود.
- به دلیل عیار بالا تقریباً در همه روشهای تولید فولاد قابل استفاده است.
تفاوت بریکت و آهن اسفنجی چیست؟
بریکت در واقع همان آهن اسفنجی است با این تفاوت که در هنگام تولید، در قطعات بزرگ قالبگیری و فشرده میشود و از آن در تولید آهن و فولاد، مواد معدنی ،مواد شیمیایی ،کودهای شیمیایی ،مواد شوینده و بهداشتی استفاده می شود.
انواع بریکت
بریکت ها در سه نوع گرم ، نرمه و سرد تولید می شوند.
- بریکت گرم : شناختهشدهترین محصول برای حملونقل آسان و ایمن آهن اسفنجی در سطح جهان بریکت گرم است که در دمای بیش از 650 درجه سانتیگراد تولید میشود.
- بریکت سرد : در فرآیند بریکت سازی سرد، مواد ورودی در دمای محیط به ماشین بریکت زنی وارد میشوند. در این فرآیند با توجه به نوع مواد ورودی به ماشین، دو نوع محصول شناختهشده است. که عبارتاند از بریکت نرمه آهن اسفنجی و بریکت سرد آهن اسفنجی.
تفاوت گندله با آهن اسفنجی چیست؟
از نظر کاربرد گندله ماده اولیه برای کوره های احیا مستقیم و کوره های بلند است تا بتوانند از آن آهن اسفنجی تولید کنند.
ریمیت آهن اسفنجی چیست؟
ریمیت آهن اسفنجی مادهای شبیه کلوخه است که پس از ذوب شدن به منظور تولید شمش، میلگرد و اسلب در صنایع فولادسازی مورد استفاده قرار میگیرد. همچنین به عنوان متریال اولیه در بسیاری از صنایع دیگر نیز کاربرد دارد.
قیمت آهن اسفنجی
قیمت روز آهن اسفنجی مانند دیگر محصولات فولادی تحت تاثیر عوامل مختلفی چون قیمت ارز ، قیمت جهانی فولاد ، میزان عرضه و تقاضا و… قرار دارد.
سخن آخر
همان طور که اشاره شد از احیای مستقیم سنگ آهن بدون ذوب کردن آن، آهن اسفنجی با عیار 67درصد به دست می آید که شکل ظاهری آن به صورت قطعات کروی متخلخل بوده و اسفنجی است. در کشور ما نیز تولید آهن اسفنجی به روش احیای مستقیم و در کوره ی الکتریکی انجام می شود و به دلیل ویژگی های منحصر به فردی که دارد به عنوان جایگزین برای ضایعات آهن به کار می رود.